Long gone are the days of extended production cycles using a single pattern or alloy. Today’s foundries, particularly those serving the automotive industry, face growing demands for flexibility, smaller batch sizes, and just-in-time delivery. These requirements go far beyond simply switching patterns — they often include complex alloy changes that must consider the chemical composition and interaction of individual elements in the melt.
Successfully managing such transitions requires deep metallurgical expertise and coordinated control across the entire production chain. From melting and alloying to pouring and quality assurance, every step must be aligned to ensure consistent quality and optimal yield.
A leading example in this area is Frankenguss in Kitzingen, Germany. Known for its extensive knowledge in metallurgy and tuned equipment, Frankenguss manages extremely tight production windows with impressive consistency.
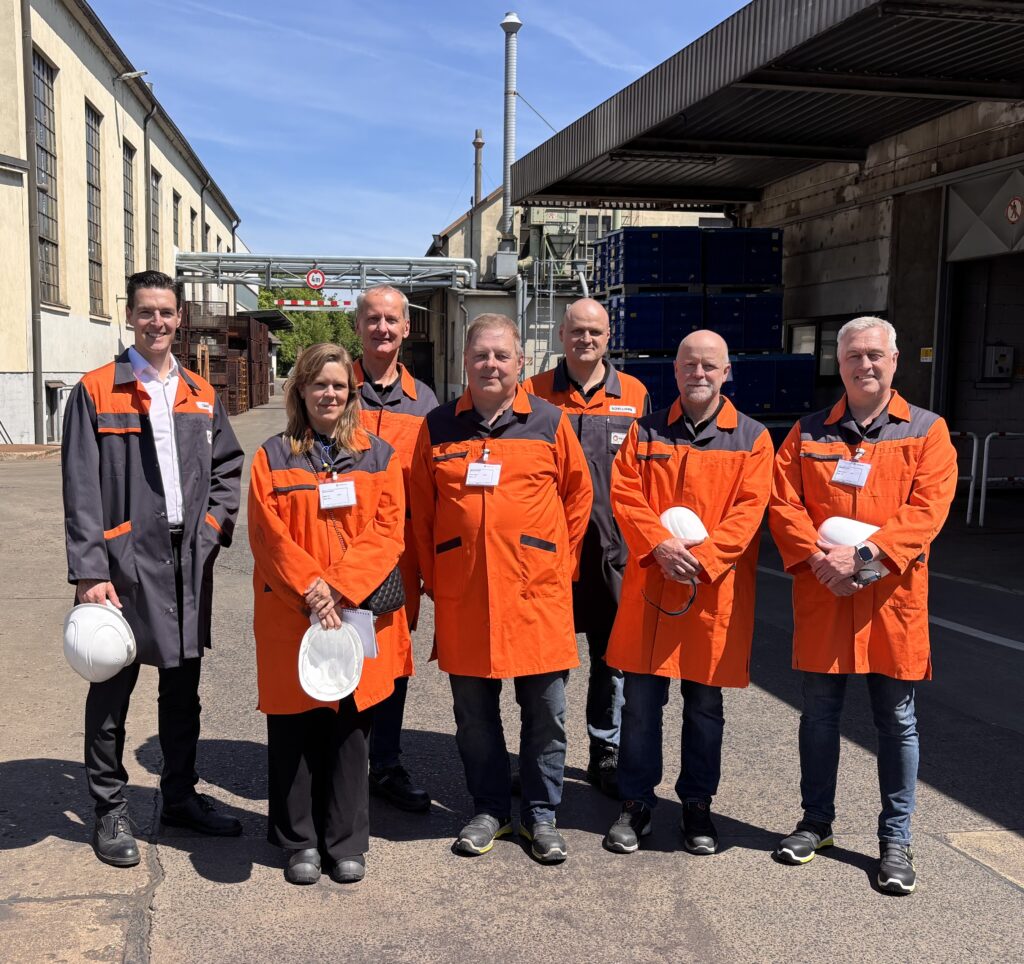
We had the pleasure of joining a delegation from Volvo’s foundry in Skövde, Sweden, for a technical visit and detailed exchange of experience at Frankenguss. The discussion focused on the production of CGI (Compacted Graphite Iron) and the alloy changes between gray iron, nodular iron, and CGI — all carried out during automatic pouring by a laser controlled unheated pouring device..
We thank Frankenguss for their warm hospitality and the valuable insights shared during this visit.