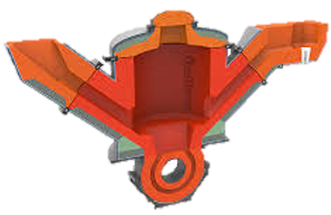
More Efficiency with the
Channel Poruing Furnace
The base of the pouring furnace is a refractory lined vessel with siphons for refilling and pouring, which can be arranged depending on the space available. The water-cooled inductor is flanged vertically to the bottom of the furnace. As soon as nitrogen or dry compressed air squeezed into the space above the metal, the liquid iron is pumped into the pour box.
During pouring, a bath level laser regulates the pressure in the furnace so that the molten iron in the pour box remains at the same level. The pouring furnace can be moved in one or two directions and can thus be positioned exactly over the pouring cup or moved away from the mold line. The furnace can be refilled without any interruptions of the pouring process. Tailormade concepts with integrated platforms ensure high ease of use and maintenance.
- Capacity 5.200 – 13.800 kg
- Power 200 – 320kW
- Overheating up to 50K/min
Perfect solution for you?
For a profitable and efficient use of the channel pouring furnace the use case, individual requirements and production properties play a decisive role. The criteria listed below provide a rough guide to check if this system is the optimal solution for you. Please note that these criteria are weighted on a case-by-case basis.
Upgrade to automation
Each of our products is designed to be equipped with software, lasers and cameras on request. Upgrade the system to speed up pouring process and work steps to a large extent with less effort at the same time. When talking about automatic pouring, we distinguish between three levels that build on one another.
The channel pouring furnace ladle can be easily upgraded at any time in order to start with a simple manual system and convert it to a sophisticated, automated system. By adding special features, it may be possible to significantly increase the production output while reducing the manpower to do it.
Not the right product?
View other products or contact us. We also customize products for various use cases!
the Channel pouring furnace
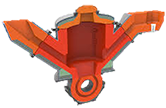
As soon as nitrogen or dry compressed air squeezed into the space above the metal, the liquid iron is pumped into the pour box.
During pouring, a bath level laser regulates the pressure in the furnace so that the molten iron in the pour box remains at the same level. The pouring furnace can be moved in one or two directions and can thus be positioned exactly over the pouring cup or moved away from the mold line. The furnace can be refilled without any interruptions of the pouring process. Tailormade concepts with integrated platforms ensure high ease of use and maintenance.
- Capacity 5.200 – 13.800 kg
- Power 200 – 320kW
- Overheating up to 50K/min
Perfect solution for you?
For a profitable and efficient use of channel pouring furnace the use case, individual requirements and production properties play a decisive role. The criteria listed below provide a rough guide to check if this system is the optimal solution for you. Please note that these criteria are weighted on a case-by-case basis.
Upgrade to Automation
These are available either as manual or (semi-) automated or intelligent solution. The system can be easily upgraded at any time to obtain a sophisticated system.
When talking about automatic pouring, we distinguish between three levels that build on one another. Upgrade the Channel Pouring Furnace to speed up pouring process and work steps to a large extent with less effort at the same time.

Semi-automatic pouring
For a solid and constant pouring process in your production.
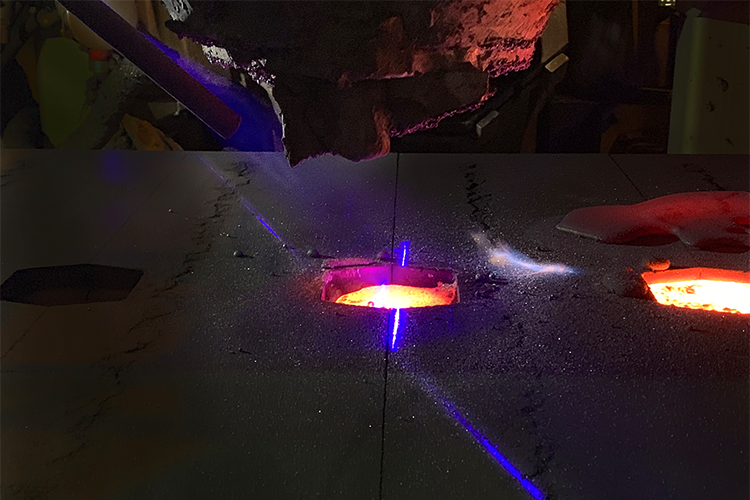
Automatic pouring
Pouring upgrade leading to a fast, independent and accurate process.
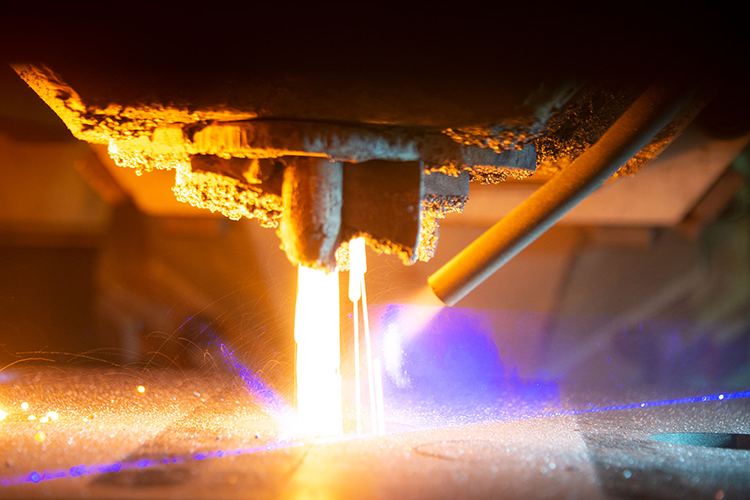
Intelligent pouring
The high-end solution for an intelligent and a self-learning production.
Not the right Product?
View other products or contact us. We also customize products for various use cases!