Intelligent pouring
The high-end solution for a self-learning production

The intelligent pourTECH™ system is equipped with an electric servo drive stopper rod actuator unit, hydraulic, pneumatic, hardware and control systems.
The system operates on horizontal and vertical mold lines, and will perform as follows:
- The PLC controls the flow of molten metal from the nozzle into the mold by opening and closing the stopper. It gets information by the laser to be able to adjust the filling speed. Using the specific parameter stored in a database, the pouring will be performed for each individual pattern.
- Control System is enhanced by Artificial Intelligence called EASYpour™.
- EASYpour™ controls and optimizes the pouring cycle by itself and communicates with the mold line. For the process itself, the operator is not needed anymore.
- The PLC will position the pouring unit with the nozzle over the pouring cup by a dedicated laser control system.
In case of Mg-treated iron a pneumatic driven stopper twist and plunger can be supplied.
Profit from automatic pouring
no adjustments needed
EASYpour™ is a self tuning system and the needed adjustemts are not necessary any more.
selflearning process
Feed back for each mold can be stored in database Due to the working with AI, the process will be improved anytime.
high relief for the operator
Operators are completely released from the repeatable work. They can do some other work during the pouring or take a break.
quality improvement
By having constant pouring conditions the quality will be improved and the scrap rate can be reduced.
profitable production
Higher output of the foundry due to higher yield.
Portfolio of intelligent pouring
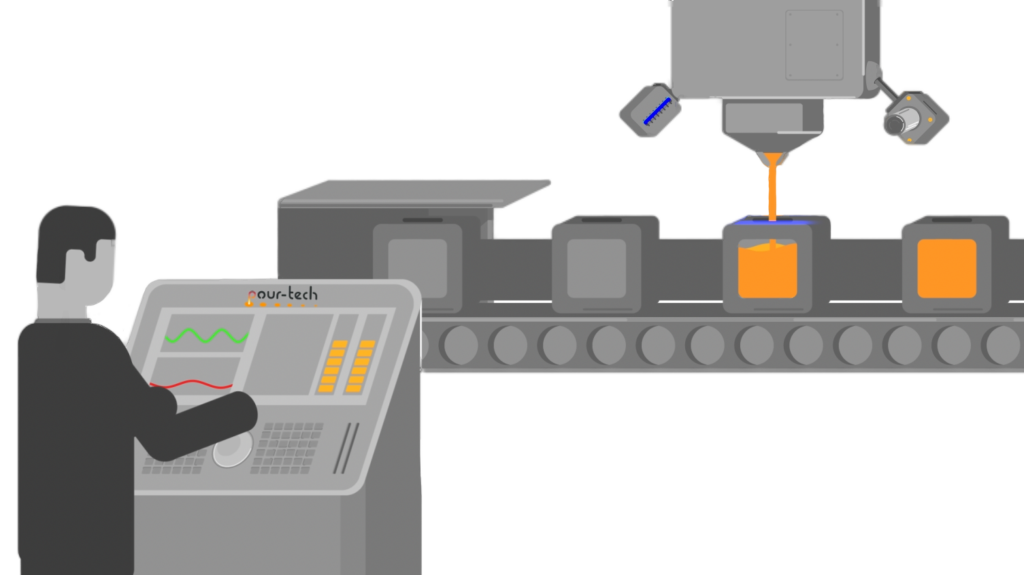
EASYpour™
No need to observe the pouring process by an operator
It is complicated getting skilled operators for one of the most important processes in the foundry – the pouring of molds. Therefore we developed a digital operator supported by Artificial Intelligence called EASYpour™. The technology is based on self-learning algorithms which monitor the current state of the pourTECH™ system together with historical data from the pourTECH™ database.
EASYpour™ controls the pouring parameters to continuously optimize the pouring and trying to maintain a high and consistent result of the pouring. For each pour, EASYpour™ will try to make the next one better or at least as good as the previous one, this enables a very high consistency in the production.
By using the new created algorithms for the system another important benefit of EASYpour™ is the improvement of quality and the reduction of pouring time. The pouring time can be kept more constant at an optimal time level. Running EASYpour™ for the very first time on a pattern, the operator only sets up two parameters and the system starts to work independently. Parameters for already known patterns can be taken from the database as well.
To run the EASYpour™ system it is necessary to install pourTECH™ database and the final level laser. All three systems work “hand in hand”. The level laser controls the pouring result (level) of any individual pouring without reducing the speed of the mold line. In case of a horizontal mold line, the final level can be measured with the pouring sensor. The database stores all data of each individual pour in a save place.
inoTECH™
Inoculation Detection
reduce inoculation material and defects
The inoTECH™ in stream inoculation detection system gives the operator the full control over the inoculation process. By using the pour-tech inoculation it detects the actual hit rate of the inoculation material into the iron stream.
A blue line laser illuminates the area of the pouring stream and creates a laser curtain. A vision camera is installed in line with the inoculation tube. When the material is leaving the tube, it must go through the laser curtain and creates flashes, which are detected and counted by the camera. inoTECH™ determines the actual hit rate with this information. The allowed tolerances can be set in the parameters. If not enough material hits the stream, the system generates an alarm, and the production will be stopped until the problem is solved.
The inoTECH™ system is fully integrated in the pourTECH™ control system. Therefore, it is not necessary to install a separate computer system.
The system allows to scroll through the last two hours of production to identify the inoculation quality of each mold. All values and pictures are stored in the pourTECH ™ Database (if installed).
The technology is constructed for all bottom pouring systems like the unheated bottom pouring ladle working with horizontal and vertical mold lines.
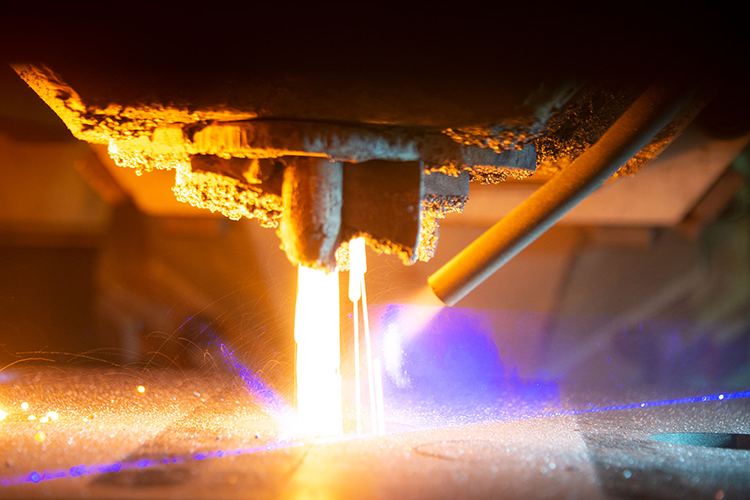
Every time the pouring device is refilled by fresh iron, an iron batch number is incremented. Typically, the iron batch number is a sequence between 1-99. The iron batch number is recorded together with the poured molds in the mold mapping register. Initially the iron batch is considered untested. When a spectrometer result is received from the test lab, the iron batch is marked approved or failed. This is done via a special screen on HMI. If an untested or failed batch reaches the end of the mold line, a signal is sent out which can be used to stop the line, light up an alarm lamp or whatever is suitable for the customer.
The mold mapping function, as standard, does not include any control of external machines or devices. However, the function can be used to also control other equipment such as automatic push outs and selection of different shake out programs. If this is required, please present your idea or request to your contact person at pour-tech.
mold mapping
Full control the whole pouring process
The mold mapping function provides monitoring of all molds currently existing along the mold line, from mold machine to shake out. Each mold is linked with information such as pouring pattern number, pouring result, pouring time, final level and iron batch. Additional information from external machines/devices can also be linked, if available. This can be for example the mold number, pour box level, mold thickness and iron temperature.
Via HMI, the operator has full access to information about each mold along the mold line. An overview screen visualizes the complete mold line, where different colours represent different statuses such as unpoured mold, good and bad poured mold. On a second screen, details about each mold can be accessed.
pourTECH™ keeps track of the ductility fade time of the iron in the pouring device. The operator restarts a timer every time the device is refilled by fresh iron. A warning is generated before a preselected time expires. If the time is exceeded, an alarm is generated and pouring stops. The fade timer is visualized on HMI.
The technology is constructed for all bottom pouring systems like the unheated bottom pouring ladle and pouring furnaces working with horizontal and vertical mold lines.
The intelligent pourTECH™ system is equipped with an electric servo drive stopper rod actuator unit, hydraulic, pneumatic, hardware and control systems.
The system operates on horizontal and vertical mold lines, and will perform as follows:
- The PLC controls the flow of molten metal from the nozzle into the mold by opening and closing the stopper. It gets information by the laser to be able to adjust the filling speed. Using the specific parameter stored in a database, the pouring will be performed for each individual pattern.
- Control System is enhanced by Artificial Intelligence called EASYpour™.
- EASYpour™ controls and optimizes the pouring cycle by itself and communicates with the mold line. For the process itself, the operator is not needed anymore.
- The PLC will position the pouring unit with the nozzle over the pouring cup by a dedicated laser control system.
In case of Mg-treated iron a pneumatic driven stopper twist and plunger can be supplied.
Profit from automatic pouring
no adjustments needed
EASYpour™ is a self tuning system and the needed adjustemts are not necessary any more.
selflearning process
Feed back for each mold can be stored in database Due to the working with AI, the process will be improved anytime.
high relief for the operator
Operators are completely released from the repeatable work. They can do some other work during the pouring or take a break.
quality improvement
By having constant pouring conditions the quality will be improved and the scrap rate can be reduced.
profitable production
Higher output of the foundry due to higher yield.
EASYpour™
no need to observe the pouring process by an operator

It is complicated getting skilled operators for one of the most important processes in the foundry – the pouring of molds. Therefore we developed a digital operator supported by Artificial Intelligence called EASYpour™. The technology is based on self-learning algorithms which monitor the current state of the pourTECH™ system together with historical data from the pourTECH™ database.
EASYpour™ controls the pouring parameters to continuously optimize the pouring and trying to maintain a high and consistent result of the pouring. For each pour, EASYpour™ will try to make the next one better or at least as good as the previous one, this enables a very high consistency in the production.
inoTECH™ Inoculation Detection
reduce inoculation material and defects
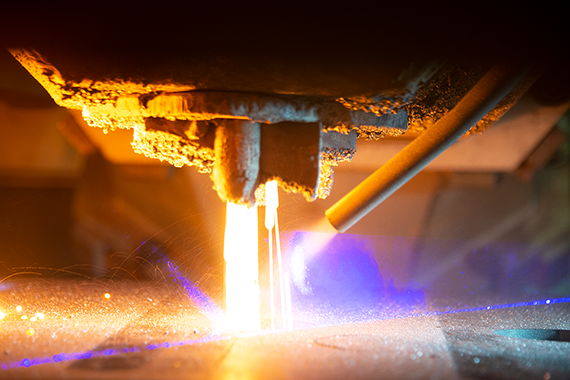
The inoTECH™ in stream inoculation detection system gives the operator the full control over the inoculation process. By using the pour-tech inoculation it detects the actual hit rate of the inoculation material into the iron stream.
A blue line laser illuminates the area of the pouring stream and creates a laser curtain. A vision camera is installed in line with the inoculation tube. When the material is leaving the tube, it must go through the laser curtain and creates flashes, which are detected and counted by the camera. inoTECH™ determines the actual hit rate with this information. The allowed tolerances can be set in the parameters. If not enough material hits the stream, the system generates an alarm, and the production will be stopped until the problem is solved.
One control system
The inoTECH™ system is fully integrated in the pourTECH™ control system. Therefore, it is not necessary to install a separate computer system. The system allows to scroll through the last two hours of production to identify the inoculation quality of each mold. All values and pictures are stored in the pourTECH ™ Database (if installed).
Mold mapping
full control of the whole pouring process
The mold mapping function provides monitoring of all molds currently existing along the mold line, from mold machine to shake out. Each mold is linked with information such as pouring pattern number, pouring result, pouring time, final level and iron batch. Additional information from external machines/devices can also be linked, if available. This can be for example the mold number, pour box level, mold thickness and iron temperature.
Visualization
Via HMI, the operator has full access to information about each mold along the mold line. An overview screen visualizes the complete mold line, where different colours represent different statuses such as unpoured mold, good and bad poured mold. On a second screen, details about each mold can be accessed.
Ductility fade timer
pourTECH™ keeps track of the ductility fade time of the iron in the pouring device. The operator restarts a timer every time the device is refilled by fresh iron. A warning is generated before a preselected time expires. If the time is exceeded, an alarm is generated and pouring stops. The fade timer is visualized on HMI.