Coreless Automatic Pouring Furnace
The Pouring Furnace for production with
frequently changing metal grades
Unique, Patented and elliptical
COIL DESIGN
made from interchangeable sections
Empties
100%
possibility to change alloys easily and to turn off the furnace during long production stops
Ultra high
Efficiency
possibility to change alloys easily and to turn off the furnace during long production stops
ABOUT
Together with our partner CIME S.r.l. (Crescenzi Induction Melting), we supply coreless induction pouring furnaces in combination with our stopper pouring control. There are more than 150 CIME pouring furnaces installed in countries all over the world at the moment. Thanks to their patented design they can be used for all metal grades and is well suited for mixed production.
TECHNICAL INFORMATION
- Capacity: 1.500 kg – 25.000 kg
- Power: 200 – 1.000 kg
- Power Efficiency: 0,9 – 1
- Overheating up to 100 K/min
perfect solution for you?
For a profitable and efficient use of the coreless automatic pouring furnace the use case, individual requirements and production properties play a decisive role. The criteria listed below provide a rough guide to check if this system is the optimal solution for you. Please note that these criteria are weighted on a case-by-case basis.
Coil made from interchangeable sections
- Each section with its own cooling, temperature control, and visualiuation on HMI
- Each section bridgeable in case of damage, no need to stop production because of damaged coil
- Each section interchangeable during maintenance
- No brazed joints that could fail
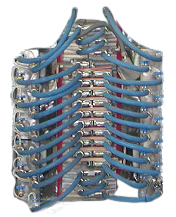
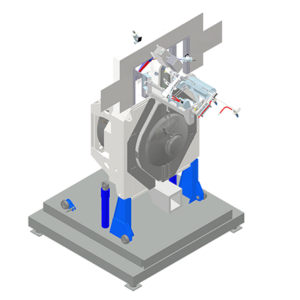
Empty 100%
- Rapid change of alloy
- Turn off power for longer stops
- Easy cleaning
Siphons inside of coil
- Constant temperature in the siphons
- More precise pouring temperature
- Siphons are easy to clean (possible to overheat for de-slagging)
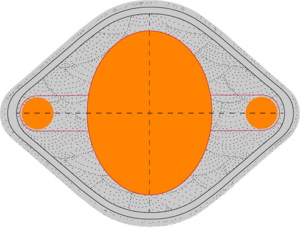
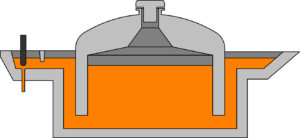
Possibility to remelt
- No need to destroy the lining after power outage
Possibility to use nitrogen
- Less magnesium fadin in ductile iron
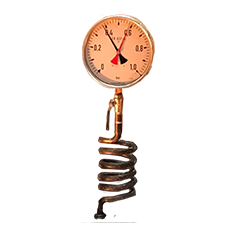
Upgrade to automation
Each of our products is designed to be equipped with software, lasers and cameras on request. Upgrade the system to speed up pouring process and work steps to a large extent with less effort at the same time. When talking about automatic pouring, we distinguish between three levels that build on one another.
The coreless pouring furncae can be easily upgraded at any time in order to start with a simple manual system and convert it to a sophisticated, automated system. By adding special features, it may be possible to significantly increase the production output while reducing the manpower to do it.
Not the right product?
View other products or contact us. We also customize products for various use cases!
Together with our partner CIME S.r.l. (Crescenzi Induction Melting), we supply coreless induction pouring furnaces in combination with our stopper pouring control. There are more than 150 CIME pouring furnaces installed in countries all over the world at the moment. Thanks to their patented design they can be used for all metal grades and is well suited for mixed production.
TECHNICAL INFORMATION
- Capacity: 1.500 kg – 25.000 kg
- Power: 200 – 1.000 kg
- Power Efficiency: 0,9 – 1
- Overheating up to 100 K/min
perfect solution for you?
For a profitable and efficient use of the coreless pouring furnace the use case, individual requirements and production properties play a decisive role. The criteria listed below provide a rough guide to check if this system is the optimal solution for you. Please note that these criteria are weighted on a case-by-case basis.
Coil made from interchangeable sections
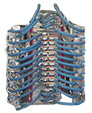
- Each section with its own cooling, temperature control, and visualiuation on HMI
- Each section bridgeable in case of damage, no need to stop production because of damaged coil
- Each section interchangeable during maintenance
- No brazed joints that could fail
Empty 100%
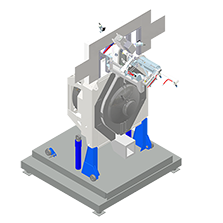
- Rapid change of alloy
- Turn off power for longer stops
- Easy cleaning
Siphons inside the coil
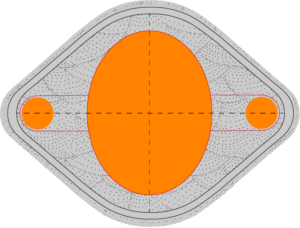
- Constant temperature in the ducts
- More precise pouring temperature
- Siphons are easy to clean (possible to overheat for de-slagging)
Possibility to remelt
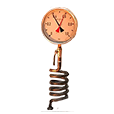
- No need to destroy the lining after power outage
Possibility to use nitrogen
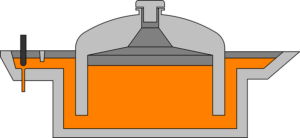
- Less magnesium fading in ductile iron
Upgrade to Automation
These are available either as manual or (semi-) automated or intelligent solution. The system can be easily upgraded at any time to obtain a sophisticated system.
When talking about automatic pouring, we distinguish between three levels that build on one another. Upgrade the Coreless Pouring Furnace to speed up pouring process and work steps to a large extent with less effort at the same time.
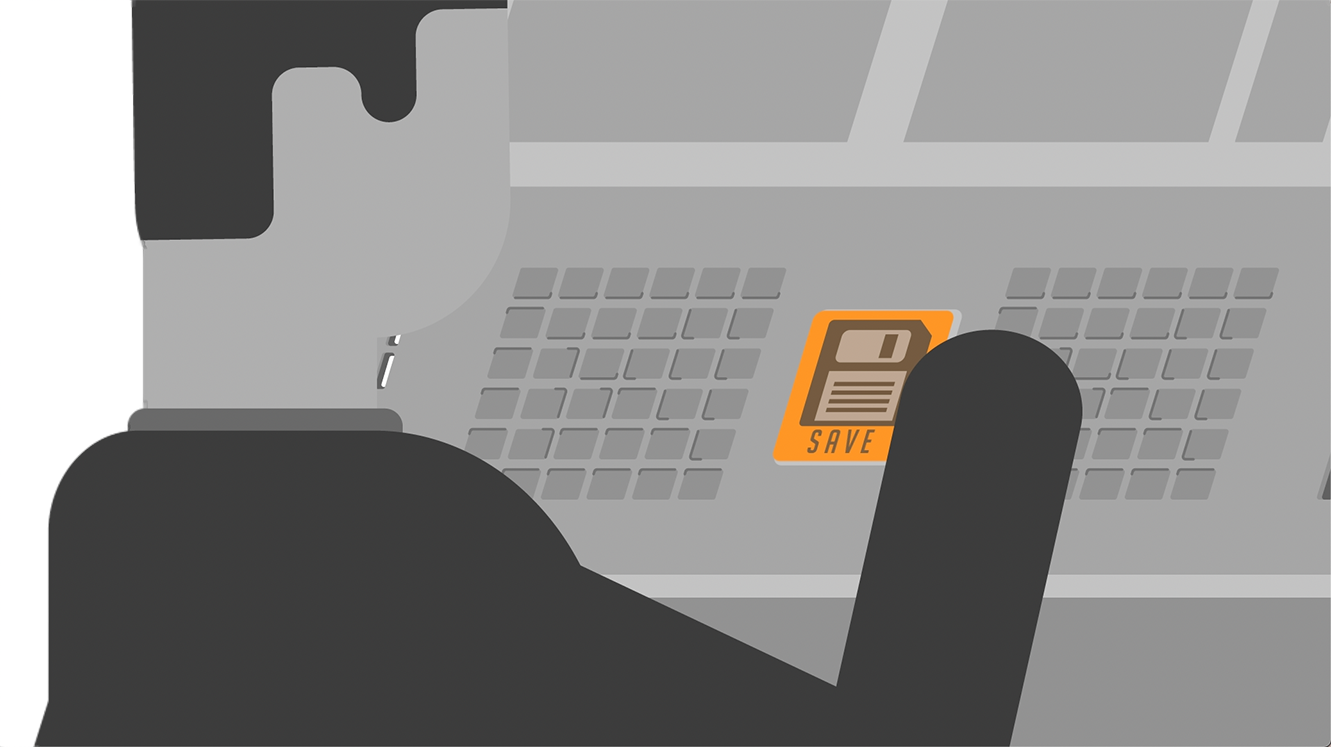
Semi-automatic pouring
For a solid and constant pouring process in your production.
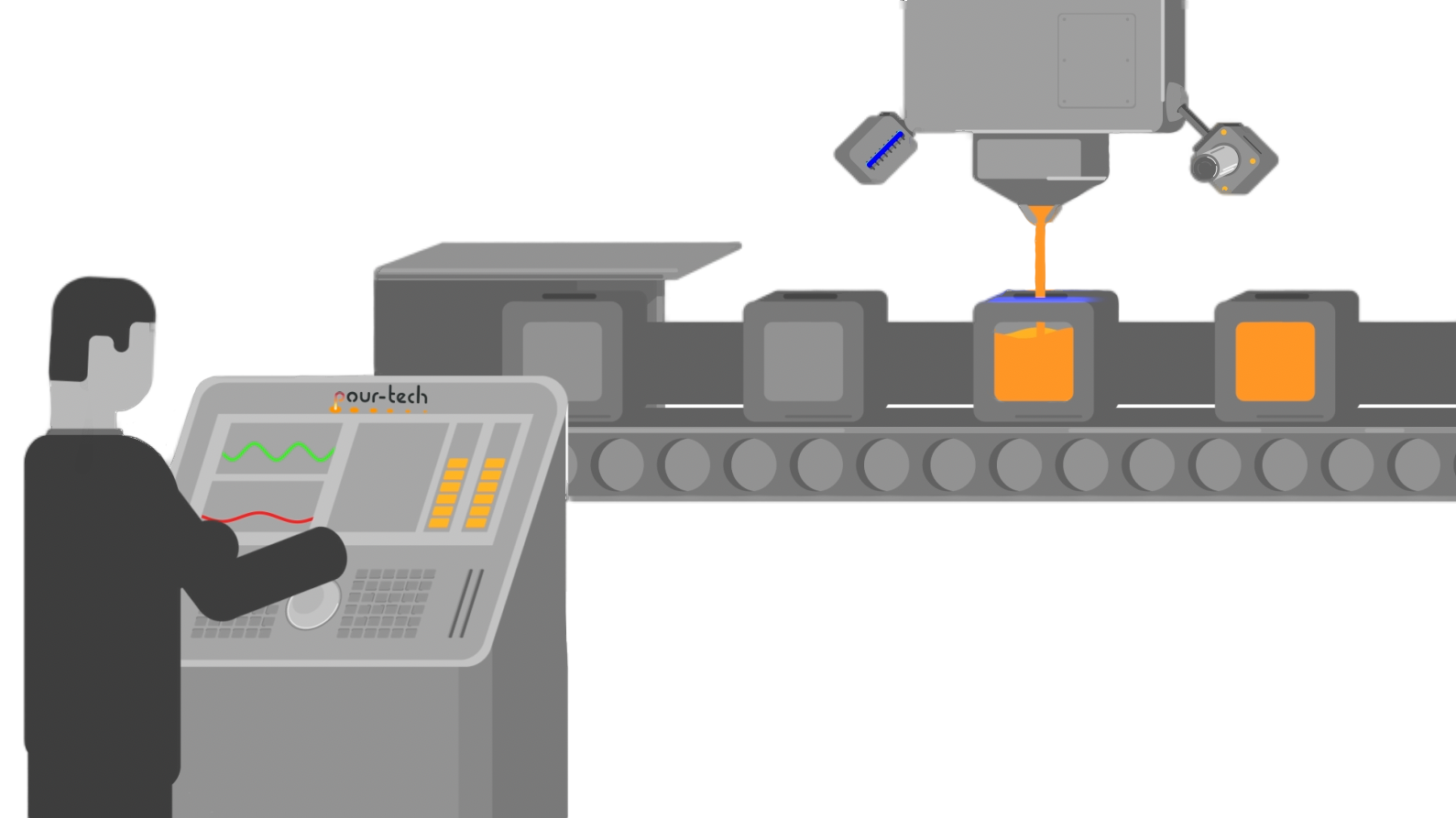
Automatic pouring
Pouring upgrade leading to a fast, independent and accurate process.
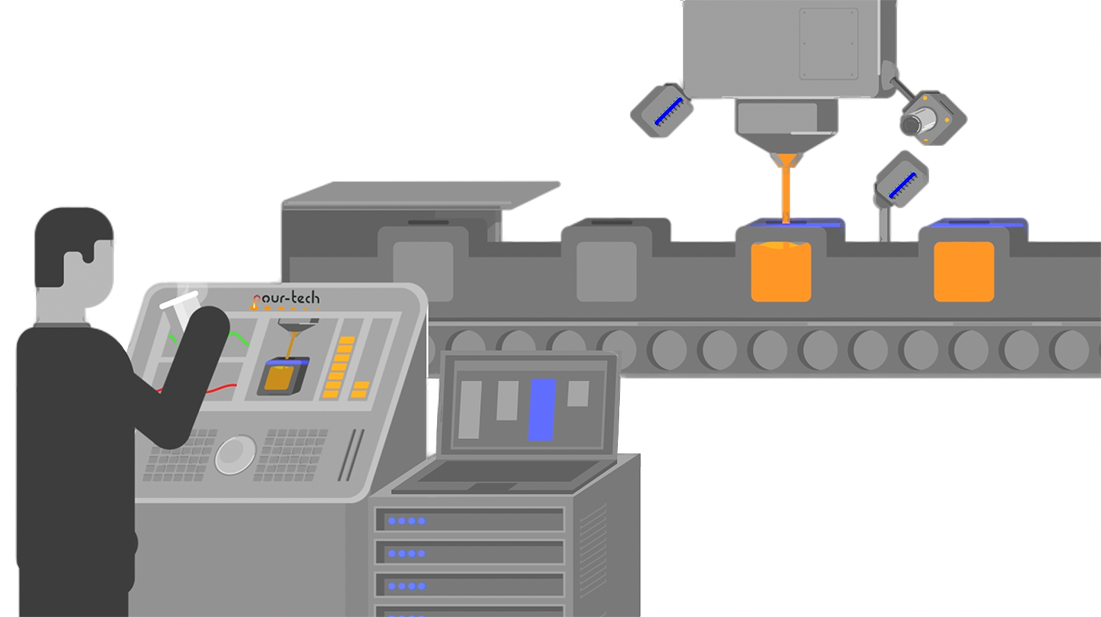
Intelligent pouring
The high-end solution for an intelligent and a self-learning production.
Not the right Product?
View other products or contact us. We also customize products for various use cases!